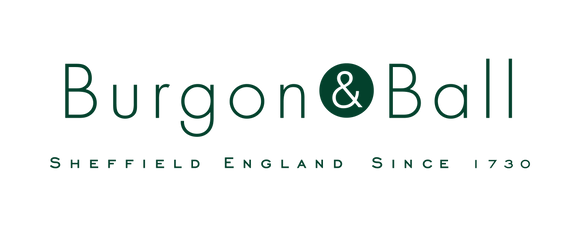
featured collections
why choose burgon & ball?
UK's leading supplier of premium garden products
With a legacy built on both superior quality and outstanding customer service, our products continue to adorn shelves in garden centers and fine retailers across Europe and other countries around the world. Now, as part of the esteemed Venanpri Tools family of heritage brands, we're poised to usher in a new era of growth and innovation globally.

1730
The business begins manufacturing agricultural shears in Sheffield, an area known since the 14th century for its skills in knives and steel.

1865
James Ball patents a manufacturing process for the production of solid steel sheep shears. The design uses the best cast steel rather than the more usual iron blades of the time. At its peak, annual production of these shears will top 300,000 pairs.

1873
Still family-run, the prospering company builds La Plata Works at Malin Bridge in Sheffield. The new factory is next to the River Loxley, which provides the power for production, until electricity later takes over.

1897
The company is now a substantial international company exporting to regions including South America, North America, Australia, the West Indies and New Zealand.

1920
Production of garden shears and equipment has now outstripped that of sheep shears. The 1922 catalogue shows over 96 designs of hoe alone!

1974
A new forge and a new despatch warehouse are completed at La Plata Works to allow more modern production systems. Further investments in manufacturing, customer service and marketing follow in the coming years.

2010
The company starts to collaborate with designer Sophie Conran, creating award-winning giftware ranges which continue to be hugely popular and extend the appeal of the Burgon & Ball brand.

2012
Burgon & Ball stainless tools are officially endorsed by the Royal Horticultural Society – possibly the ultimate accolade in the gardening industry.

2018
Burgon & Ball joins the Venanpri global family of the finest heritage tool brands. Together Burgon & Ball, Corona and Bellota represent nearly 500 years of advancement in developing superior tools and have been the leading choice for generations of horticulturalists.

grade of steel: a fine balance
Adding carbon to steel gives strength, adding chromium brings rust resistance. But it’s a trade-off; our steel cannot be high carbon and high chromium, so we make sure we get the right steel composition for each part of the tool.
A single hand fork contains three different compositions of steel:
1. Ferrule
High chromium/low carbon. Why? It starts life as a disc, so we don’t want this to be too hard because we want to shape it. It doesn’t need strength for its end function.
2. Tang
Medium chromium/medium carbon. Why? It needs to be strong to resist bending, but is also made from quite thick material to give good levels of inherent strength.
3. Tines
Low chromium/maximal carbon. Why? Tines are the weakest part of the tool, yet need maximum strength and hardness to resist bending in the ground.
Design: A Key Consideration
Our beautiful tools feature curves in all the right places. But the shaping is about more than style; it either adds extra strength, or reduces weight by allowing us to use thinner steel while maintaining strength.
Thickness: Light But Strong
We look at how the tools will be used. A spade or axe needs a thicker gauge of steel than a knife, which can be of much thinner steel. We reduce the weight wherever possible to give tools that are a pleasure to use.

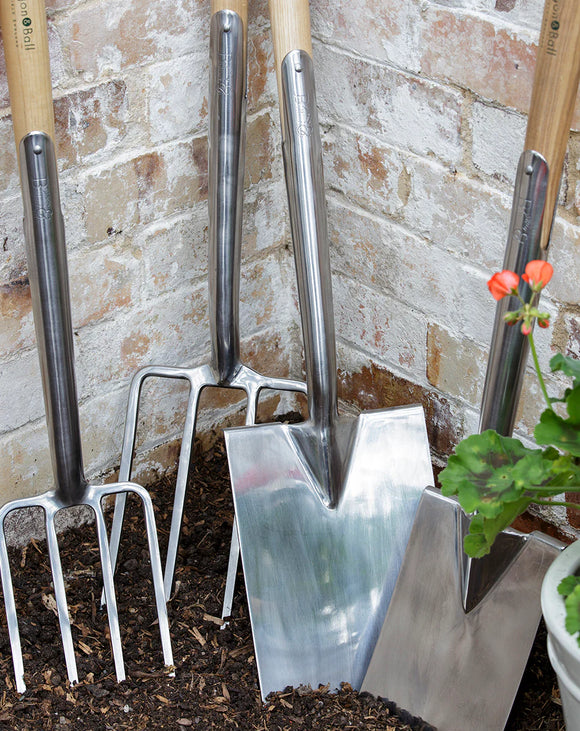
Manufacturing process: Going the extra mile
Our manufacturing processes create the most durable tools available. We make sure our welds are carried out expertly, to create joints that are actually stronger than the surrounding steel. And the tines on our large forks are hot rolled, a process which aligns the grain structure of the metal to give outstanding strength and bend resistance. Rolled tines are very unusual in stainless steel tool production – the norm is to simply cut the tines to length, weld together and grind the ends to a point.
Temperature: Turning up the heat
We carefully control the heat treatment and tempering of our steel to give exactly the right hardness for each tool’s job. Too hard and the metal may snap or chip; not hard enough and it will bend or lose its edge. We test our tools using the Rockwell scale to measure hardness by firing a diamond penetrator into the steel and calculating the indentation.
Finishing: The Final Touch
Any roughness on the surface can make even stainless steel corrode; moisture can collect in the tiny abrasions, creating a chemical reaction with the air. We make sure our tools are perfectly ground and polished to prevent this.
Consistency: Tried, Tested, Trusted
But we don’t stop there. Rigorous testing gives complete peace of mind; every batch of tools is tested against the British Standard, which determines the weight the tools must be able to withstand without permanent deformation.
And if ever a batch were to fail… we wouldn’t sell it.
